Something amazing is happening in the battery world: Battery recycling rates are steadily rising thanks to smart industry initiatives and consumer awareness.
Take the lead-acid batteries that power our cars, for starters. The industry reports a 99% recycling rate for these batteries in the U.S. — about twice the recycling rate of aluminum cans. According to a study by Battery Council International, lead car batteries are the single most recycled consumer product. That's right — about 160 million lead batteries are collected and recycled each year, according to BCI, keeping more than 2.5 million tons of lead and plastic from clogging up landfills.
But it wasn't always this way.

A few decades ago, a little more than half of lead batteries were recycled. But through coordinated efforts between battery makers, recyclers, and governments, the infrastructure and incentives emerged to make lead battery recycling not just viable, but expected. It took patience and investment, but the industry transformed battery recycling from an afterthought into a shining example of the circular economy.
As we look forward to a future with more and more lithium-ion batteries (LiB) powering everything from our phones to the latest electric vehicles, the lead battery's success story gives reason for optimism even while current LiB recycling rates languish around 5% to 15%.
As electric vehicle adoption grows in the coming decades, LiB waste is expected to exceed 20 million tons per year by 2040. This seems daunting, but it also represents a huge opportunity if we can ramp up recycling efforts. Many look at the tidal wave of spent batteries and simply see
a wall of waste. But the scrap heap of today is the gold mine of tomorrow if we have the patience and ingenuity to extract from it.
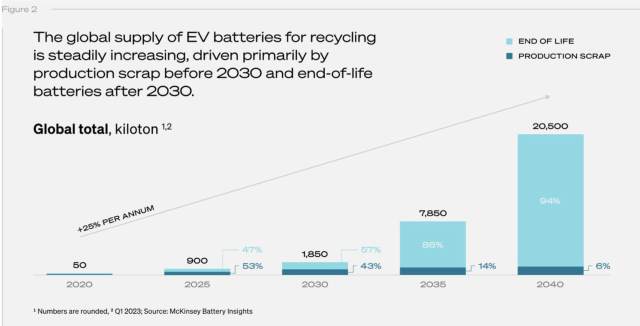
Recycling any complex product is hard. It takes time to figure out the logistics and economics. Challenges abound, especially when it comes to collecting and transporting used batteries. But we have a template, and the incentives are there to invest in solving the problems.
The recovered value in these batteries is immense. Businesses are already working to scale up LiB recycling. This is one of the reasons we're excited about the investment in Redwood Materials and their recycling infrastructure, which can extract and reenter valuable materials into the battery supply chain. This Series D raise of more than $1 billion was on the heels of Redwood Materials' $2 billion loan from the Department of Energy, giving the company ample capital to continue investing in scaling up capacity.

This won't happen overnight. We need to build the infrastructure and scale up processes. Automakers, battery producers, and recyclers must collaborate across a complex value chain. Persistence and problem-solving are required.
Looking at the humble lead battery for inspiration may seem archaic, but the iconic lead battery is a marvel of recyclability by design. Its three main components — lead, plastic, and acid — are engineered to be recycled over and over in closed-loop perfection.
This is recycling not as an afterthought, but as the core principle. Lead batteries aren't discarded; they're reborn. The typical new lead battery is formed from 80% recycled material, with no loss of performance, just the cycle continuing. Remarkably, 83% of the lead that these batteries need is sourced in North America, not from distant mines. The plastic casings also find new life. All of it circulates in near-perfect loops.
Over decades, lead batteries have woven a network of manufacturing, collection sites, and recyclers across the country, with more than 300,000 locations accepting used batteries. It's an ecosystem designed to keep lead circulating. This didn't happen overnight. Industry groups brought stakeholders together to slowly build smart systems and instill responsible battery management. No hype, just persistence.
The benefits of recycling go beyond reducing waste. Recycled lead requires 70% less energy to produce than mining and smelting new lead ore. Less energy means less carbon pollution. Recycling completes the loop. Lead batteries have shown a path forward and according to research by McKinsey & Company, there's hope that LiB can follow a similar track.
Replicating the lead recycling pipeline for LIBs will not be straightforward. Unfortunately, the process of recycling an LIB is inherently trickier than it is for a lead battery. Lead is the only metal in a lead acid battery, and it can be separated from the rest of the battery materials with a simple process that yields high-purity ingots. Compare this to an LIB, in which the valuable metals are numerous and varied and exist in chemical mixtures that generally require more sophisticated separation methods.
Lead car batteries are a recycling success story, but the ubiquitous single-use alkaline batteries that power our flashlights and TV remotes have followed a less inspiring path. Recycling rates for these batteries remain quite low, buoyed only by regulations that incentivize otherwise noneconomic practices. A key problem is that the metals that make up an alkaline battery — mainly iron, zinc, and manganese — are so darn cheap.
Luckily for LiBs, the lithium, nickel, and cobalt that make up the bulk of material costs are quite valuable. This, combined with the massive and growing LIB market, gives us hope that LIB recycling can become profitable at scale.
Driven by this prize and the goal of increasing EV sustainability, startups like Redwood Materials are addressing the technological challenges of separation. Processes like theirs are able to recover, on average, around 95% or more of battery materials for reuse at falling costs. That's valuable metal pulled back from the brink to offset the need for costly new mining.

It will take some time before recycled LIB materials can steal significant market share from mined minerals. The problem is that EV adoption is growing too fast for new battery demand to be matched by a supply of old batteries. From 2021 to 2022, the share of new car purchases that were EVs increased from 8.7% to 14% globally and from 4.5% to 7.7% in the U.S. As far as problems go, this is a good one to have, and it should certainly not discourage activity in the LIB recycling space. Estimates are that recycling will satisfy about 7% of lithium and 11% of cobalt and nickel demand in 2030 and about double that a decade later.
The most exciting thing is that we are just now nearing a critical mass when the volume of LIBs ending their service life can justify investment in building recycling gigafactories. By 2025, we should have enough recyclable battery material to manufacture >100GWh of new LIBs. And thanks to the Inflation Reduction Act of 2022, battery recycling is benefiting due to a clause in the legislation titled the "Advanced Manufacturing Production Credit," which grants 10 years' worth of tax credits for the domestic manufacturing of battery cells and modules. With this clause, batteries recycled in the U.S. qualify for subsidies, no matter the batteries' origin.
Importantly, the prospect of a dual-stream market for these battery materials may benefit recyclers. If recyclers are able to lower costs (including regulatory incentives to promote the greener practice), but aren't able to supply the entire industry, then they can demand prices that reflect the high costs of mined material, leading to higher profits. Increasing the value of an end-of-life LIB may reduce the total cost of ownership for an EV, further growing the EV market.
The monetary profit "generated per ton of battery material could approach approximately $600 by as early as 2025," according to a recent McKinsey & Company study. Going forward, McKinsey says it "expects the value creation potential to grow to similar levels to the primary metals industry, which is around 30% depending on price developments."

In addition to better recycling techniques and infrastructure, there are significant opportunities in creating new kinds of batteries that are not only optimized for particular use cases, but are also longer lasting and safer. For example, Byterat provides an end-to-end cloud platform for battery research and engineering. In turn, this helps the industry build better, longer-lasting batteries. Similarly, Zitara offers powerful battery management software to help better understand, manage, and maximize batteries. By extending battery life, we can reduce the amount of batteries entering recycling in the first place.
Recycling this coming wave of LiB is no small challenge. But we've faced this crossroads before and transformed problems into progress through patient investment. If we apply those lessons, battery recycling could quietly blossom into a pillar of the circular economy — just when we need it most.
The incentives align for recycling to become the norm, not the exception. But it takes vision to see value in discarded batteries and perseverance to extract it. If we maintain that mindset, LiB recycling has the potential to be a quiet triumph that supports sustainability.
Most things that matter take patience and persistence. Battery recycling is no exception. But with the mindset that transformed lead battery recycling, we can transform recycling for LiB and other technologies.
Often, the most important progress goes unnoticed precisely because it becomes so widely adopted that we take it for granted. We forget how much effort went into making recycling not just viable, but normal.
Battery recycling likely won't make headlines. But it's a quiet triumph and an encouraging reminder of our ability to build smart circular systems if we put our minds to it.
Teddy Albertson is a Science Advisor at Collab Fund supporting technologies and startups that will change the world. He has a PhD in Applied Physics from Caltech and was previously a NASA Space Technology Research Fellow.
Andrew Montgomery is a Partner at Collab Fund investing in early-stage companies pushing the world forward. He is a former founder, finance, and M&A operator, and has over 10 years venture investing experience.
Join our free newsletter for weekly updates on the coolest innovations improving our lives and saving our planet.